Технологія виготовлення деталей на токарному верстаті. Точіння деталей циліндричної форми
На головну
розділ п'ятий
Основні операції і роботи,
виконувані на токарному верстаті
глава XI
Обточування зовнішніх циліндричних поверхонь
На токарних верстатах можна обробляти деталі, поверхні яких мають форму тіл обертання. Більшість деталей, що застосовуються в машинобудуванні, має циліндричні поверхні, як, наприклад, валики, втулки і ін.
1. Різці для поздовжнього обточування
Для поздовжнього обточування застосовують прохідні різці. Прохідні різці поділяються на чорнові і чистові.
Чорнові різці (рис. 99) призначені для грубого обточування - обдирання, виробленої з метою швидко зняти зайвий метал; їх називають часто обдирного. Такі різці виготовляють зазвичай з привареною або припаяної, або з механічно прикріпленою платівкою і постачають довгою ріжучої крайкою. Вершину різця заокруглені по радіусу r \u003d 1-2 мм. На рис. 99, а показаний різець чорновий прохідний прямий, а на рис. 99, б - відігнутий. Відігнута форма різця дуже зручна при обтачивании поверхонь деталей, що знаходяться біля кулачків патрона, і для підрізання торців. Після обточування чорновим різцем поверхню деталі має великі ризики; якість обробленої поверхні виходить внаслідок цього низьким.
Чистові різці служать для остаточного обточування деталей, т. Е. Для отримання точних розмірів і чистої, рівної поверхні обробки. існують різні види чистових різців.
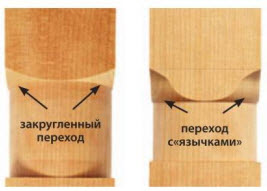
На рис. 100, а показаний чистової прохідний різець, що відрізняється від чорнового головним чином великим радіусом заокруглення, рівним 2-5 мм. Цей тип різця застосовується при чистових роботах, які виробляються з невеликою глибиною різання і малою подачею. На рис. 100, б показаний чистової різець з широкою ріжучої крайкою, паралельної осі оброблюваної деталі. Такий різець дозволяє знімати чистову стружку при великій подачі і дає чисту і гладко оброблену поверхню. На рис. 100, в показаний різець В. Колесова, який дозволяє отримувати чисту і гладко оброблену поверхню при роботі з великою подачею (1,5-3 мм / об) при глибині різання 1-2 мм (див. Рис. 62).
2. Встановлення і закріплення різця
Перед обточування потрібно правильно встановити різець в резцедержателе, стежачи за тим, щоб виступаюча з нього частину різця була можливо коротше - не більш 1,5 висоти його стержня.
При більшому вильоті різець при роботі буде тремтіти, в результаті оброблена поверхня вийде нерівною, хвилястою, зі слідами дроблення.
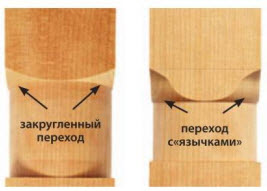
На рис. 101 показана правильна і неправильна установка різця в різцетримачі.
У більшості випадків рекомендується встановлювати вершину різця на висоті центрів верстата. Для цього застосовують підкладки (максимум двох), поміщаючи їх під всією опорною поверхнею різця. підкладка є плоскою сталеву лінійку довжиною 150-200 мм, що має строго паралельні верхню і нижню поверхні. Токар повинен мати набір таких підкладок різної товщини, щоб отримати необхідну для установки різця висоту. Не слід для цієї мети користуватися випадковими пластинками.
Підкладки треба ставити під різець так, як показано на рис. 102 зверху.
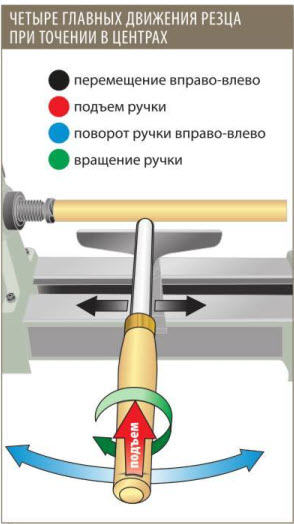
Для перевірки стану вершини різця по висоті підводять вершину його до одного з попередньо вивірених центрів, як показано на рис. 103. Для цієї ж мети можна користуватися рискою, проведеної на пінолі задньої бабки, на висоті центру.
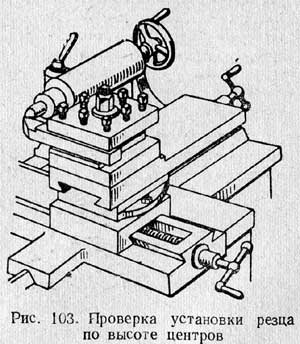
Закріплення різця в різцетримачі має бути надійним і міцним: різець повинен бути закріплений не менш ніж двома болтами. Болти, що закріплюють різець, повинні бути рівномірно і туго затягнуті.
3. Установка і закріплення деталей в центрах
Поширеним способом обробки деталей на токарних верстатах є обробка в центрах (Рис. 104). При цьому способі в торцях оброблюваної деталі попередньо засверливают центрові отвори - центруют деталь. При установці на верстаті в ці отвори входять вістря центрів передньої і задньої бабок верстата. Для передачі обертання від шпинделя передньої бабки до оброблюваної деталі застосовується диск приводу 1 (рис. 104), Навинчивающийся на шпиндель верстата, і хомутик 2, який закріплюється гвинтом 3 на оброблюваної деталі.
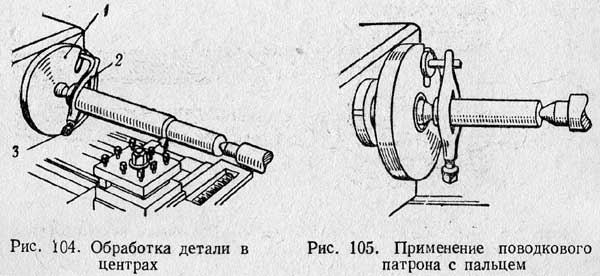
Вільним кінцем хомутик захоплюється пазом (рис. 104) або пальцем (рис. 105) патрона і призводить деталь в обертання. У першому випадку хомутик робиться відігнутим (рис. 104), у другому - прямим (рис. 105). Диск приводу з пальцем, показаний на рис. 105, становить небезпеку для робочого; безпечнішим є диск приводу із запобіжним кожухом (рис. 106).
Істотними приладдям токарного верстата є центри. Зазвичай застосовується центр, показаний на рис. 107, а.
Він складається з конуса 1, на який встановлюється деталь, і конічного хвостовика 2. Хвостовик повинен точно підходити до коническому отвору шпинделя передньої бабки і пінолі задньої бабки верстата.
Передній центр обертається разом зі шпинделем і оброблюваної деталлю, тоді як центр задньої бабки в більшості випадків нерухомий і треться об обертову деталь. Від тертя нагріваються і зношуються як конічна поверхня центру, так і поверхню центрового отвору деталі. Для зменшення тертя необхідно змащувати задній центр.
При обточування деталей на великих швидкостях, а також при обробці важких деталей робота на нерухомому центрі задньої бабки неможлива через швидкого зносу самого центру і розробки центрового отвори.
У цих випадках застосовують обертові центри. На рис. 108 показана одна з конструкцій обертового центру, що вставляється в конічний отвір пінолі задньої бабки. Центр 1 обертається в кулькових підшипниках 2 і 4. Осьовий тиск сприймається наполегливим кульковим підшипником 5. Конический хвостовик 3 корпусу центру відповідає коническому отвору пиноли.
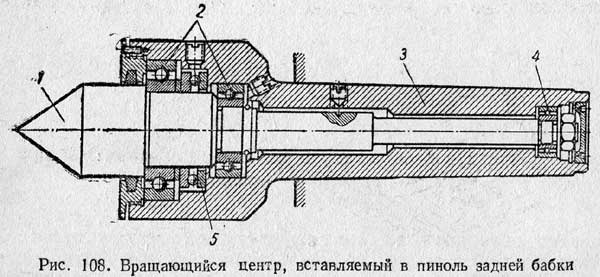
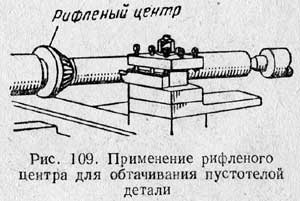
Для скорочення часу на закріплення деталей замість хомутиков з ручним затиском часто застосовують рифлені передні центри (Рис. 109), які не тільки центруют деталь, але і виконують роль повідця. При натиску заднім центром рифлення врізаються в оброблювану деталь і цим передають їй обертання. Для порожнистих деталей застосовують зовнішні (рис. 110, а), а для валиків-внутрішні (зворотні) рифлені центри (рис. 110, б).
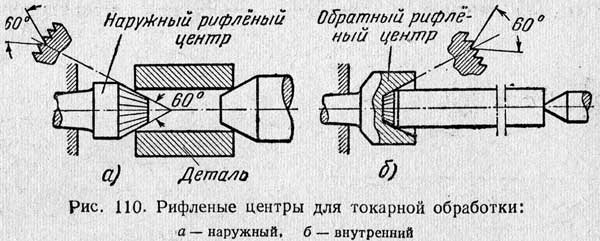
Такий спосіб кріплення дозволяє обточувати деталь по всій довжині за одну установку. Обточування тих же деталей зі звичайним центром і хомутиком може бути зроблено тільки за дві установки, що значно збільшує час обробки.
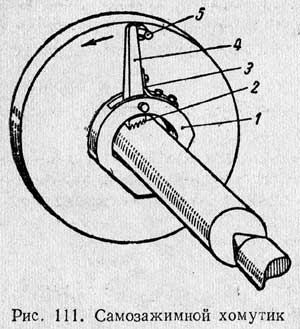
Для легких і середніх токарних робіт застосовують самозажімние хомутики. Один з таких хомутиков зображений на рис. 111. В корпусі 1 такого хомутика на осі встановлений кулачок 4, кінець якого має рифлену поверхню 2. Після установки хомутика на деталь рифлена поверхню кулачка під дією пружини 3 притискається до деталі. Після установки в центри та пуску верстата палець 5 диску приводу, натискаючи на кулачок 4, заклинює деталь і приводить її в обертання. Такі самозажімние хомутики значно скорочують допоміжний час.
4. Налагодження верстата для обробки в центрах
Для отримання циліндричної поверхні при обтачивании заготовки в центрах необхідно, щоб передній і завдань центри знаходилися на осі обертання шпинделя, а різець переміщався паралельно цій осі. Щоб перевірити правильність розташування центрів, потрібно наблизити задній центр до переднього (рис. 112). Якщо вістря центрів не збігаються, необхідно відрегулювати положення корпуса задньої бабки на плиті, як було зазначено на стор. 127.
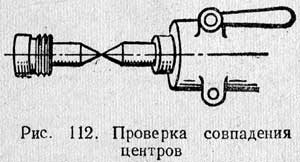
Розбіжність центрів може бути також викликано потраплянням бруду або стружки в конічні отвори шпинделя або пі-нулі. Щоб уникнути цього, необхідно перед установкою центрів ретельно протерти отвори шпинделя і пінолі, а також конічну частину центрів. Якщо центр передньої бабки і після цього, як кажуть, «б'є», значить він несправний і повинен бути замінений іншим.
При точінні деталь нагрівається і подовжується, створюючи при цьому посилений тиск на центри. Щоб уберегти деталь від можливого вигину, а задній центр - від заїдання, рекомендується час від часу звільняти задній центр, а потім знову його підтискати до нормального стану. Необхідно також періодично додатково змащувати заднє центровий отвір деталі.
5. Установка і закріплення деталей в патронах
Короткі деталі зазвичай встановлюють і закріплюють в патронах, які поділяються на прості і трикулачні.
Прості патрони виготовляють зазвичай чотирикулачні (рис. 113). У таких патронах кожен кулачок 1, 2, 3 і 4 переміщається своїм гвинтом 5 незалежно від інших. Це дозволяє встановлювати і закріплювати в них різні деталі як циліндричної, так і нециліндричної форми. При установці деталі в чотирикулачні патроні необхідно її ретельно вивірити, щоб вона не била при обертанні.
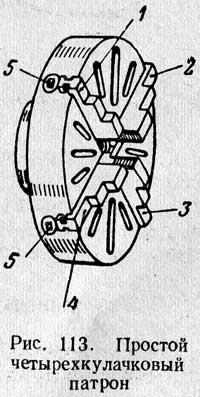
Вивірку деталі при її установці можна виробляти за допомогою рейсмас. Чертилку рейсмас підводять до перевіряється поверхні, залишаючи між ними зазор в 0,3-0,5 мм; повертаючи шпиндель, стежать за тим, як змінюється цей зазор. За результатами спостереження віджимають одні кулачки і підтискають інші до тих пір, поки зазор не стане рівномірним по всьому колу деталі. Після цього деталь остаточно закріплюють.
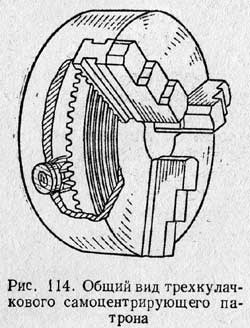
трикулачні патрони (Рис. 114 і 115) в більшості випадків застосовуються трикулачні, значно рідше - Двомуфтовий. Ці патрони дуже зручні в роботі, так як всі кулачки в них переміщаються одночасно, завдяки чому деталь, що має циліндричну поверхню (зовнішню чи внутрішню), встановлюється і затискається точно по осі шпинделя; крім того, значно скорочується час на установку і закріплення деталі.
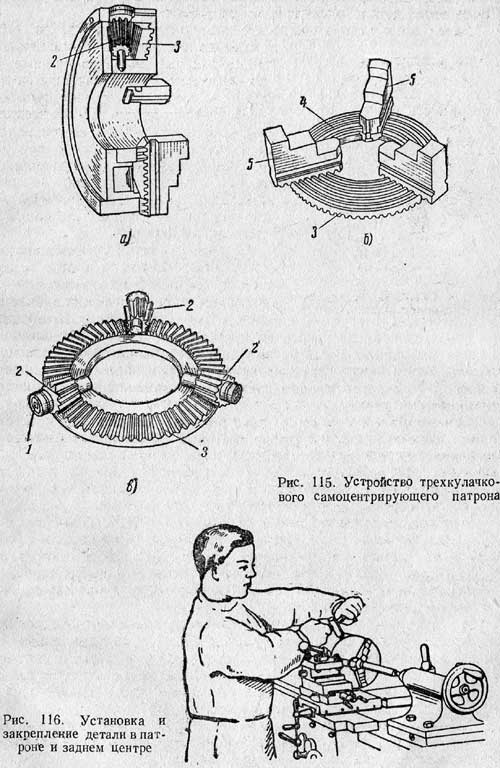
У ньому кулачки переміщаються за допомогою ключа, який вставляють в чотиригранний отвір 1 одного з трьох конічних зубчастих коліс 2 (рис. 115, в). Ці колеса зчеплені з великим конічним колесом 3 (рис. 115, б). На зворотному плоскій стороні цього колеса нарізана багатовиткова спіральна канавка 4 (рис. 115, б). В окремі витки цієї канавки входять своїми нижніми виступами все три кулачка 5. Коли ключем повертають одне з зубчастих коліс 2, обертання передається колесу 3, яке, обертаючись, за допомогою спіральної канавки 4 переміщує по пазах корпусу патрона одночасно і рівномірно все три кулачка. При обертанні диска зі спіральною канавкою в ту або іншу сторону кулачки наближаються або віддаляються від центру, відповідно затискаючи або звільняючи деталь.
Необхідно стежити, щоб деталь була міцно закріплена в кулачках патрона. Якщо патрон в справному стані, то міцний затиск деталі забезпечується застосуванням ключа з короткою ручкою (рис. 116). Інші способи затиску, наприклад зажим за допомогою ключа і довгої труби, що надівається на ручку, ні в якому разі не повинні допускатися.
кулачки патронів. Кулачки застосовують загартовані і сирі. Зазвичай користуються загартованими кулачками через їхню малу зношуваності. Але при затиску такими кулачками деталей з чисто обробленими поверхнями на деталях залишаються сліди у вигляді вм'ятин від кулачків. Щоб уникнути цього рекомендується застосовувати також і сирі (незагартовані) кулачки.
Сирі кулачки зручні ще й тим, що їх можна періодично розточувати різцем і усувати биття патрона, яке неминуче з'являється при тривалій його роботі.
Установка і закріплення деталей в патроні з підтримкою заднім центром. Цей спосіб застосовується при обробці довгих і порівняно тонких деталей (рис. 116), які недостатньо закріпити тільки в патроні, так як зусилля від різця і вага виступаючої частини можуть зігнути деталь і вирвати її з патрона.
цангові патрони. Для швидкого закріплення коротких деталей невеликого діаметра за зовнішню оброблену поверхню застосовують цангові патрони. Такий патрон показаний на рис. 117. Конічним хвостовиком 1 патрон встановлюється в конічному отворі шпинделя передньої бабки. У виточенні патрона встановлена \u200b\u200bрозрізна пружна втулка 2 з конусом, звана цангою. В отвір 4 цанги вставляють оброблювану деталь. Потім навертають на корпус патрона за допомогою ключа гайку 3. При навернення гайки пружна цанга стискається і закріплює деталь.
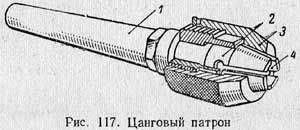
пневматичні патрони. На рис. 118 показана схема пневматичного патрона, який забезпечує швидке і надійне закріплення деталей.
На лівому кінці шпинделя закріплений повітряний циліндр, усередині якого є поршень. Стиснене повітря по трубках надходить в центральні канали 1 і 2, звідки направляється в праву або ліву порожнину циліндра. Якщо повітря надходить по каналу 1 в ліву порожнину циліндра, то поршень витісняє повітря з правої порожнини циліндра по каналу 2 і навпаки. Поршень пов'язаний зі штоком 3, сполученим зі штангою 4 і повзуном 5, який діє на довгі плечі 6 колінчастих важелів, короткі плечі 7 яких переміщують затискні кулачки 8 патрона.
Довжина ходу кулачків складає 3-5 мм. Тиск повітря зазвичай 4-5 am. Для приведення в дію пневматичного циліндра на корпусі коробки швидкостей встановлюється розподільний кран 9, що повертається рукояткою 10.
6. нагвинчуванні і згвинчення кулачкових патронів
Перш ніж нагвинчувати патрон на шпиндель, необхідно ретельно протерти ганчіркою різьблення на кінці шпинделя і в отворі патрона і потім змастити їх маслом. Легкий патрон підносять обома руками безпосередньо до кінця шпинделя і нагвинчують його до відмови (рис. 119). Важкий патрон рекомендується покласти на дошку (рис. 120), підвівши його отвір до кінця шпинделя, нагвинчують патрон до відмови, як і в першому випадку, вручну. При нагвинчуванні патрона потрібно стежити за тим, щоб осі патрона і шпинделя строго збігалися.
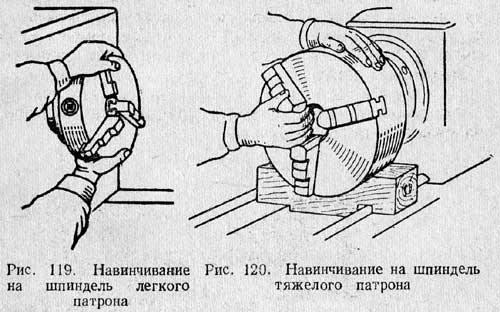
Для попередження випадків самовідгвинчування патронів в верстатах для швидкісного різання застосовують додаткове закріплення патрона на шпинделі за допомогою різних пристроїв
(Загвинчування додаткової гайки, закріплення патрона фасонними сухарями і ін.).
Згвинчення патрона проводиться таким чином. Вставляють в патрон ключ і обома руками виробляють ривок на себе (рис. 121).
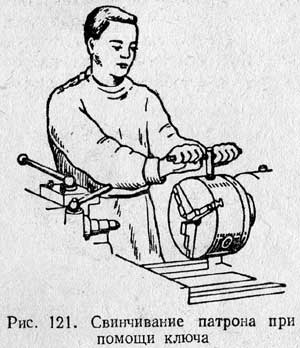
Інші способи свинчивания, пов'язані з різкими ударами по патрону або по кулачкам, неприпустимі: патрон пошкоджується, кулачки в його корпусі розхитуються.
Загвинчування і згвинчення важкого патрона краще виробляти, вдаючись до допомоги підсобного робітника.
7. Прийоми обточування гладких циліндричних поверхонь
Обточування циліндричних поверхонь зазвичай виробляють в два етапи: спочатку знімають начорно більшу частину припуску (3-5 мм на діаметр), а потім решту (1-2 мм на діаметр).
Щоб отримати заданий діаметр деталі, необхідно встановити різець на необхідну глибину різання. Для установки різця на глибину різання можна застосувати спосіб пробних стружок або користуватися лімбом поперечної подачі.
Для установки різця на глибину різання (на розмір) способом пробних стружок необхідно:
1. Повідомити деталі обертальний рух.
2. Обертанням маховичка поздовжньої подачі та рукоятки гвинта поперечної подачі вручну підвести різець до правого торця деталі так, щоб його вершина торкнулася поверхні деталі.
3. Встановивши момент торкання, відвести вручну різець вправо від деталі і обертанням рукоятки гвинта поперечної подачі перемістити різець на потрібну глибину різання. Після цього обточують деталь з ручною подачею на довжині 3-5 мм, зупиняють верстат і вимірюють діаметр обточеної поверхні штангенциркулем (рис. 122). Якщо діаметр вийде більше необхідного, різець відводять вправо і встановлюють його на трохи більшу глибину, знову протачивают поясок і знову роблять вимір. Все це повторюють до тих пір, поки не буде отримано заданий розмір. Тоді включають механічну подачу і обточують деталь по всій заданій довжині. Після закінчення вимикають механічну подачу, відводять різець назад і зупиняють верстат.
У такому ж порядку проводять чистове обточування.
Користування лімбом гвинта поперечної подачі. Для прискорення установки різця на глибину різання у більшості токарних верстатів є спеціальне пристосування. Воно розташоване у рукоятки гвинта поперечної подачі і являє собою втулку або кільце, на колі якого нанесені поділки (рис. 123). Ця втулка з поділами називається лімбом. Ділення відраховують по ризику, наявної на нерухомій втулці гвинта (на рис. 123 ця ризику збігається з 30-м штрихом лімба).
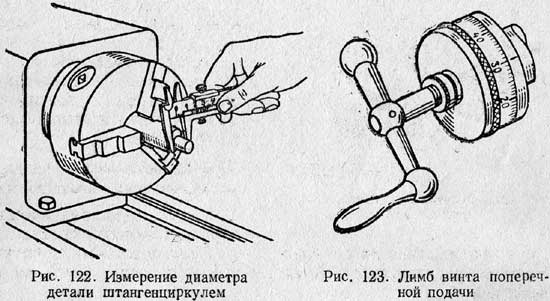
Число поділок на лімбі і крок гвинта можуть бути різними, отже, різної буде і величина поперечного переміщення різця при повороті лімба на одну поділку. Припустимо, що лімб розділений на 100 рівних частин, а гвинт поперечної подачі має різьблення з кроком 5 мм. При одному повному обороті рукоятки гвинта, т. Е. На 100 поділок лімба, різець переміститься в поперечному напрямку на 5 мм. Якщо ж повернути рукоятку на одну поділку, то переміщення різця складе 5: 100 \u003d 0,05 мм.
Слід мати на увазі, що при переміщенні різця в поперечному напрямку радіус деталі після проходу різця зменшиться на таку ж величину, а діаметр деталі - на подвоєну. Таким чином, для того щоб зменшити діаметр деталі, наприклад з 50,2 до 48,4 мм, т. Е. На 50,2 - 48,4 \u003d 1,8 мм, необхідно перемістити різець вперед на половинну величину, т. Е . на 0,9 мм.
Встановлюючи різець на глибину різання за допомогою лімба гвинта поперечної подачі, необхідно, однак, враховувати зазор між гвинтом і гайкою, який утворює так званий «мертвий хід». Якщо упустити це з виду, то діаметр обробленої деталі буде відрізнятися від заданого.
Тому при установці різця на глибину різання за допомогою лімба необхідно дотримуватися такого правила. Завжди підходити до необхідної установці по лімбу повільним правим обертанням рукоятки гвинта (рис. 124, а; необхідна установка - 30-е поділ лімба).
Якщо ж повернути рукоятку гвинта поперечної подачі на величину більше необхідної (рис. 124, б), то для виправлення помилки ні в якому разі не подавати рукоятку назад на величину помилки, а потрібно зробити майже повний оборот в зворотну сторону, а потім обертати рукоятку знову вправо до необхідного розподілу по лімбу (рис. 124, в). Так само роблять, коли треба відвести різець назад; обертаючи рукоятку вліво, відводять різець більш ніж це потрібно, а потім правим обертанням підводять до необхідного поділу лімба.
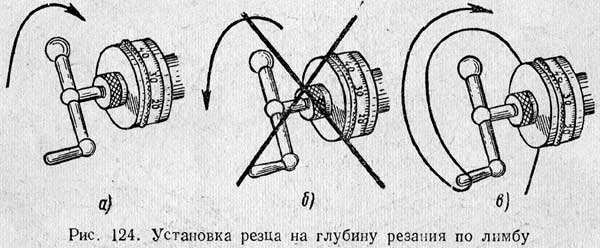
Переміщення різця, відповідне одному поділу лімба, на різних верстатах різному. Тому, приступаючи до роботи, необхідно визначити величину переміщення, що відповідає на даному верстаті одному поділу лімба.
Користуючись лімба, наші токарі-швидкісник домагаються отримання заданого розміру і без пробних стружок.
8. Обробка деталей в люнетах
Довгі і тонкі деталі, довжина яких в 10-12 разів більше їх діаметра, при обтачивании прогинаються як від власної ваги, так і від зусилля різання. В результаті деталь отримує неправильну форму - в середині вона виявляється товщі, а по кінцях - тонше. Уникнути цього можна, застосувавши особливе підтримує пристосування, зване люнетом. При застосуванні люнетів можна обточувати деталі з високою точністю і знімати стружку більшого перетину, не побоюючись прогину деталі. Люнети б, шают нерухомі і рухомі.
нерухомий люнет (Рис. 125) має чавунний корпус 1, з яких за допомогою відкидного болта 7 скріплюється відкидна кришка 6, що полегшує установку деталі. Корпус люнета внизу оброблений відповідно до форми напрямних станини, на яких він закріплюється за допомогою планки 9 і болта 8. У отворах корпусу за допомогою регулювальних болтів 3 переміщаються два кулачка 4, а на даху - один кулачок 5. Для закріплення кулачків в необхідному положенні служать гвинти 2 . Такий пристрій дозволяє встановлювати в люнет вали різних діаметрів.
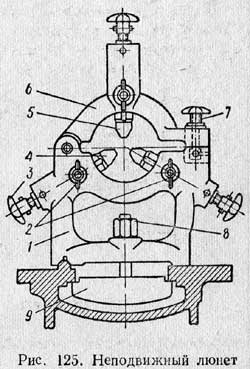
Перш ніж встановити необточені заготовку в нерухомий люнет, потрібно проточити у неї посередині канавку під кулачки шириною трохи більше ширини кулачка (рис. 126). Якщо заготовка має велику довжину і малий діаметр, то при цьому неминучий її прогин. Щоб уникнути цього протачивают додаткову канавку ближче до кінця заготовки і, встановивши в ній люнет, протачивают основну канавку посередині.
Нерухомі люнети застосовують також для відрізання кінців і підрізання торців у довгих деталей. На рис. 127 показано використання нерухомого люнета при підрізання торця: деталь закріплена одним кінцем в трикулачні патроні, а іншим встановлена \u200b\u200bв люнете.
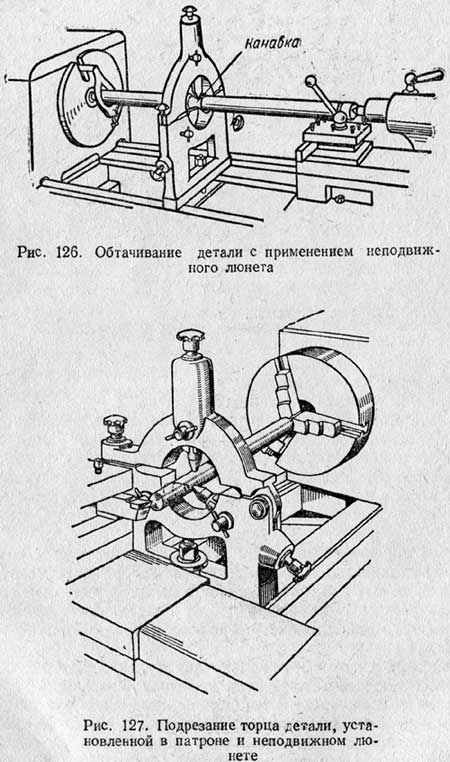
Таким же чином можна обробити точний отвір з торця довгої деталі, наприклад, розточити конічний отвір в шпинделі токарного верстата або просвердлити таку деталь по всій її довжині.
рухомий люнет (Рис. 128) використовують при чистовому обточування довгих деталей. Люнет закріплюють на каретці супорта так, що він разом з нею переміщується вздовж обточувати деталі, слідуючи за різцем. Таким чином, він підтримує деталь безпосередньо в місці додатка зусилля і оберігає деталь від прогинів.
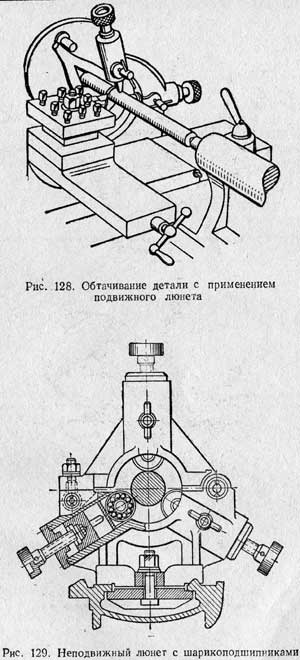
Рухомий люнет має тільки два кулачка. Їх висувають і закріплюють так само, як кулачки нерухомого люнета.
Люнети зі звичайними кулачками не придатні для швидкісної обробки через швидке зношення кулачків. У таких випадках застосовують люнети з роликовими або кульковими підшипниками (Рис. 129) замість звичайних кулачків, завдяки чому полегшується робота роликів і зменшується нагрівання оброблюваної деталі.
9. Прийоми обточування циліндричних поверхонь з уступами
При обробці на токарних верстатах партії деталей ступінчастою форми (ступінчасті валики) з однаковою довжиною у всіх деталей окремих ступенів новатори в цілях скорочення часу на вимірювання довжини застосовують поздовжній упор, що обмежує переміщення різця, і лімб поздовжньої подачі.
Використання поздовжнього упору. На рис. 130 показаний поздовжній упор. Він закріплюється болтами на передній спрямовуючої станини, як показано на рис. 131; місце закріплення упору залежить від довжини обточувати ділянки деталі.
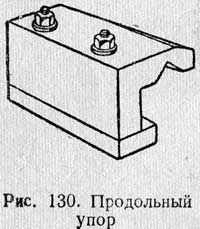
При наявності на верстаті поздовжнього упору можна обробляти циліндричні поверхні з уступами без попередньої розмітки, при цьому, наприклад, ступінчасті валики обтачиваются за одну установку значно швидше, ніж без упору. Досягається це укладанням між упором і супортом обмежувача довжини (мірної плитки), відповідного по довжині щаблі валика.
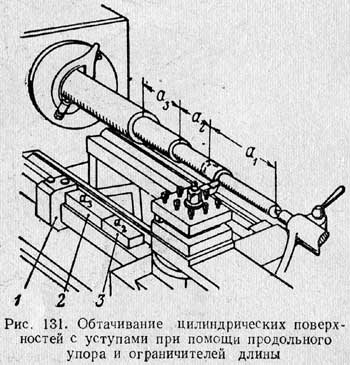
Приклад обточування ступеневої валика за допомогою упору 1 і мірних плиток 2 і 3 показаний на ріс.131. Обточування ступені а 1 проводиться до тих пір, поки супорт не впреться в мірну плитку 3. Знявши цю плитку, можна обточувати наступний щабель валика довжиною а 2 до моменту, коли супорт впреться в плитку 2. Нарешті, знявши плитку 2, протачивают щабель а 3 . Як тільки супорт дійде до упору, необхідно вимкнути механічну подачу. Довжина мірної плитки 2 дорівнює довжині уступу a 3, а довжина плитки 3 - відповідно довжині уступу а 2.
Застосовувати жорсткі упори можна тільки на верстатах, що мають автоматичне вимикання подачі при перевантаженні (наприклад, 1А62 і інші нові системи верстатів). Якщо верстат такого пристрою не має, то виробляти обточування по упору можна тільки за умови завчасного виключення механічної подачі і доведення супорта до упору уручну, інакше неминуча поломка верстата.
Використання лімба поздовжньої подачі Використання лімба поздовжньої подачі. Для скорочення часу, що витрачається на вимірювання довжин оброблюваних деталей, на сучасних токарних верстатах встановлено лімб поздовжньої подачі. Цей лімб представляє обертовий диск великого діаметра (рис. 132), розташований на передній стінці фартуха і за маховичком поздовжньої подачі. На окружність диска нанесені рівні поділу. При обертанні маховичка повертається і лімб, пов'язаний зубчастої передачею з колесом поздовжньої подачі. Таким чином, визначеному подовжньому переміщенню супорта з різцем відповідає поворот лімба на певне число поділок відносно нерухомої ризики.
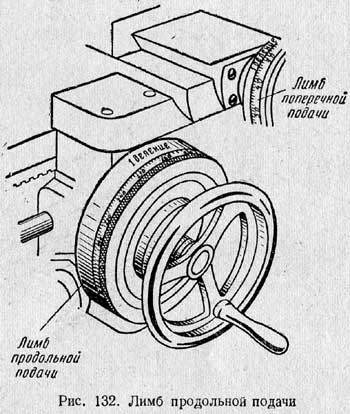
При обробці східчастих деталей використання лімба поздовжньої подачі досить раціонально. В цьому випадку токар перед обробкою першої деталі з партії планує попередньо різцем за допомогою штангенциркуля довжину ступенів, а потім починає їх обточувати. Обточити першу сходинку, він встановлює поздовжній лімб в нульове положення відносно нерухомої ризики. Обточуючи наступні ступені, він запам'ятовує (або записує) відповідні свідчення лімба відносно тієї ж ризики. Обточуючи наступні деталі, токар користується показаннями, встановленими при обтачивании першої деталі.
Використання поперечного упора. Для скорочення часу, що витрачається на вимірювання діаметрів при обробці східчастих деталей, на ряді токарних верстатів можливе використання поперечного упора.
Один з таких упорів показаний на рис. 133. Упор складається з двох частин. Нерухому частину 1 встановлюють на каретці і закріплюють болтами 2; завзятий штифт 6 нерухомий. Рухомий наголос 3 встановлюють і закріплюють болтами 4 на нижній частині супорта. Гвинт 5 встановлюють точно на необхідний розмір деталі. Кінець гвинта 5, впираючись в штифт 6, зумовлює необхідний розмір деталі. Помістивши між штифтом 6 і гвинтом 5 мірні плитки, можна виробляти обточування деталі зі ступенями різних діаметрів.

10. Режими різання при обточуванні
Вибір глибини різання. Глибину різання при обточуванні вибирають в залежності від припуску на обробку та виду обробки - чорновий або чистової (див. Стор. 101-102).
Вибір величини подачі. Подачу також вибирають в залежності від виду обробки. Зазвичай приймають подачу при чорновому обточуванні від 0,3 до 1,5 мм / об, а при напівчистове і чистовому від 0,1 до 0,3 мм / об при роботі нормальними різцями і 1,5-3 мм / об при роботі різцями конструкції В. Колесова.
Вибір швидкості різання. Швидкість різання зазвичай вибирають за спеціально розробленими таблицями в залежності від стійкості різця, якості оброблюваного матеріалу, матеріалу різця, глибини різання, подачі, виду охолодження та ін. (Див., Наприклад, табл. 6, стор. 106).
11. Брак при обтачивании циліндричних поверхонь і заходи щодо його запобігання
При обточування циліндричних поверхонь можливі наступні види шлюбу:
1) частину поверхні деталі залишилася необробленої;
2) розміри обточеної поверхні невірні;
3) обточена поверхню вийшла конічної;
4) обточена поверхню вийшла овальної;
5) чистота обробленої поверхні не відповідає вказівкам в кресленні;
6) згоряння заднього центру;
7) розбіжність поверхонь при обробці валика в центрах з двох сторін.
1. Брак першого виду досягається за рахунок недостатніх розмірів заготовки (недостатнього припуску на обробку), поганий правки (кривизна) заготовки, неправильної установки і неточною вивірки деталі, неточного розташування центрових отворів і зміщення заднього центра.
2. Невірні розміри обточеної поверхні можливі при неточною установці різця на глибину різання або неправильному вимірі деталі при знятті пробної стружки. Усунути причини цього виду шлюбу можна і треба підвищенням уваги токаря до виконуваної роботи.
3. Конусность обточеної поверхні виходить зазвичай в результаті зсуву заднього центру щодо переднього. Для усунення причини цього виду шлюбу необхідно правильно встановити задній центр. Звичайною причиною зсуву заднього центру є потрапляння бруду або дрібної стружки в конічний отвір пінолі. Очищенням центру і конічного отвору пиноли можна усунути і цю причину шлюбу. Якщо ж і після очищення вістря переднього і заднього центрів не збігаються, треба відповідно перемістити корпус задньої бабки на її плиті.
4. Овальність обточеної деталі виходить при битті шпинделя через нерівномірне вироблення його підшипників або нерівномірного зносу його шийок.
5. Недостатня чистота поверхні при обтачивании може бути по ряду причин: велика подача різця, застосування різця з неправильними кутами, погано загострено різця, малий радіус заокруглення вершини різця, велика в'язкість матеріалу деталі, тремтіння різця через велику вильоту, недостатньо міцне кріплення різця в резцедержателе, збільшені зазори між окремими частинами супорта, тремтіння деталі через нетривкого кріплення її або внаслідок зносу підшипників і шийок шпинделя.
Всі перераховані причини браку можуть бути своєчасно усунені.
6. Від згоряння жорсткого центра задньої бабки може бути викликано наступними причинами: занадто туго закріплена деталь між центрами; погана мастило центрового отвору; неправильна зацентровка заготовки; висока швидкість різання.
7. Розбіжність поверхонь обробки при обтачивании з двох сторін в центрах виходить головним чином як наслідок биття переднього центру або розробки центрових отворів у заготівлі. Для запобігання браку необхідно при чистової обробки перевірити стан центрових отворів заготовки, а також стежити за тим, щоб не було биття центру передньої бабки.
12. Техніка безпеки при обтачивании циліндричних поверхонь
У всіх випадках обробки на токарних верстатах необхідно звертати увагу на міцне закріплення деталі і різця.
Надійність кріплення деталі, що обробляється в центрах, в значній мірі залежить від стану центрів. Не можна працювати зі зношеними центрами, так як деталь під дією зусилля різання може бути вирвана з центрів, відлетіти в сторону і нанести токареві поранення.
При обробці деталей в центрах і патронах виступаючі частини хомутика і кулачки патрона нерідко захоплюють одяг робітника. Ці ж частини можуть бути причиною пошкодження рук при вимірюванні деталі і прибирання верстата на ходу. Для попередження нещасних випадків слід влаштовувати у хомутиков запобіжні щитки або застосовувати безпечні хомутики, а кулачкові патрони захищати. Досконалий тип безпечного хомутика показаний на рис. 134. Обід 3 прикриває не тільки головку болта 2, але і палець 1 диску приводу.
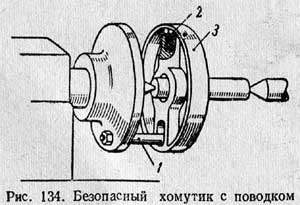
Для захисту рук і одягу токаря від виступаючих частин патрона або планшайби на сучасних токарних верстатах застосовується спеціальне огородження (рис. 135). Кожух 1 пристосування шарнірно з'єднаний з пальцем 2, закріпленим на корпусі передньої бабки.
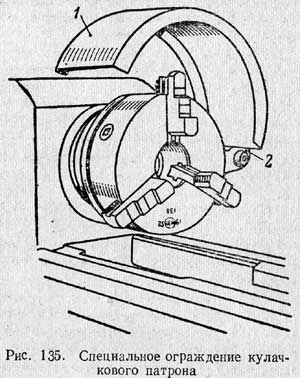
При установці деталей в центрах потрібно звертати увагу на правильність центрових отворів. При недостатній їх глибині деталь під час обертання може зірватися з центрів, що дуже небезпечно. Точно так же, закріпивши деталь в патроні, треба перевірити, виймуть чи ключ. Якщо ключ залишився в патроні, то при обертанні шпинделя він вдариться об станину і відлетить убік. У цьому випадку можливі й поломка верстата, і нанесення поранення робітникові.
Причиною нещасних випадків часто є стружка, особливо зливна, яка при високих швидкостях різання сходить безперервною стрічкою. Таку стружку ні в якому разі не можна видаляти або обривати руками, вона може заподіяти сильні порізи і опіки. Слід у всіх можливих випадках застосовувати стружколоматель. В крайньому випадку, коли ламання стружки не досягається, слід видаляти її спеціальним гачком.
При обробці матеріалів, що дають коротку відскакує стружку, необхідно користуватися захисними окулярами або застосовувати запобіжні щитки з небиткого скла або целулоїду (рис. 136), що прикріплюються на шарнірної стійки до каретки. Змітати дрібну стружку, яка утворюється при обробці тендітних металів (чавуну, твердої бронзи), потрібно не руками, а щіткою.
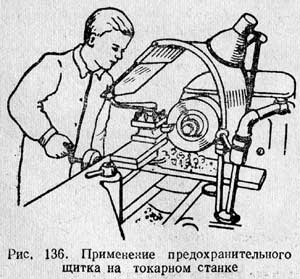
Можливі поранення рук при установці і закріпленні різців в результаті зриву ключа з головок кріпильних болтів резцедержателя. Зрив ключа відбувається при зношених губах ключа і голівках болтів. Часто, однак, зрив відбувається і від того, що токар користується ключем, розмір якого не відповідає розміру болта.
Установка різця по висоті центрів за допомогою будь-якого роду не пристосованих для цього підкладок (металевих обрізків, шматочків ножівок і т. П.) Не забезпечує стійкого положення різця під час його роботи. Під тиском стружки такі підкладки зміщуються, і установка різця розладжується. При цьому слабшає і кріплення різця. В результаті підкладки і різець можуть вискочити з резцедержателя і поранити токаря. Крім того, під час установки різця і при роботі на верстаті можливі пошкодження рук об гострі кромки металевих підкладок. Тому рекомендується кожному токареві мати набір підкладок, різних за товщиною, з добре обробленими опорними площинами і краями.
Контрольні питання 1. Як правильно встановити різець в резцедержателе?
2. Як перевірити стан вершини різця щодо лінії центрів?
3. Як встановлюють і закріплюють деталі при обтачивании циліндричних поверхонь?
4. У чому відмінність між умовами роботи переднього і заднього центрів?
5. Як влаштований обертається центр і в яких випадках його застосовують?
6. Як влаштований рифлений передній центр і в чому його переваги?
7. Як перевірити правильність установки центрів для обточування циліндричної поверхні?
8. Як влаштований самоцентрує патрон? Назвіть його деталі, правила установки і підготовки його до роботи.
9. Як зробити вивірку деталі при її установці в чотирикулачні патроні?
10. Яке призначення лімба гвинта поперечної подачі?
11. Для чого служить лімб поздовжньої подачі? Як він влаштований?
12. Для чого служать люнети і в яких випадках вони застосовуються?
13. Як влаштований нерухомий люнет?
14. Як влаштований рухливий люнет?
15. Як підготовляється заготовка вала для установки в люнет?
16. Наведіть приклад використання поздовжнього упору; поперечного упора.
17. Які види шлюбу можливі при обтачивании циліндричних поверхонь? Як усунути причини браку?
18. Перерахуйте основні правила техніки безпеки при обтачивании циліндричних поверхонь.
Технологія виготовлення деталей на токарному верстаті. |
Виготовлення будь-якої деталі починають з підбору матеріалу. Відібраний матеріал нарізають на заготовки. Розмір заготовки завжди перевищує розміри готової деталі на деяку величину (припуск). Величина і форма припуску залежать від форми деталі, технології її виготовлення. |
Для точіння найкраще підходить однорідна за текстурою деревина. Це береза, липа, осика, бук, в'яз, горіх. Точіння деталі на центрових верстатах
|
Мал. 1. Послідовність точіння деталі а- закріплення заготовки; б - закріплення заготовки розріз; в- чорнова обробка Рейєр; г-чистове обробка Мейселем; д обрізка (торцювання) заготовки. Виточування внутрішніх порожнин Для виточування внутрішніх поверхонь заготовку закріплюють тільки в передній бабці верстата, кулачковим патроном, планшайбою або трубчастим патроном.
|
|
Мал. 2. Точіння порожнистих виробів а- на планшайбе; б-в трубчастому патроні. Робота на токарних верстатах з супортом На токарних верстатах з супортом обробка ведеться різцями закріпленими в резцедержателе, встановленому на рухомому супорті верстата. Подібні верстати, як правило, мають ручну і механічну подачу вздовж і поперек верстата. Токарні різці. За формою головки різці підрозділяються на прямі з прямолінійним стержнем (рис. 3 а) і відігнуті зі стрижнем відігнутим в право або вліво. По розташуванню ріжучої кромки розрізняють праві (рис.3 г) і ліві (рис. 3 в) різці. Праві переміщаються в поздовжньому напрямку від задньої бабки до передньої, ліві від передньої до задньої. Прохідні різці (рис. 3 а-в) призначені для обточування, освіти фасок, прохідні упорні різці (рис.3 г) для обточування і обробки утвореного торця ступені. Підрізні різці (рис. 3 д) служать для утворення ступені на торці оброблюваної заготовки, для обробки площині торця. Канавки на зовнішній і внутрішньої поверхні деталі можна отримати за допомогою канавкових різців (рис. 3 е, з). Для відрізки застосовуються відрізні різці (рис. 3 ж). Для нарізування різьблення використовують різьбовій різець (рис. 3 і). фасонні різці заточені за формою оброблюваної деталі (рис. 3 к). |
![]() |
Мал. 3. Основні види токарних різців Різці встановлюють, так щоб вершина різця збігалася з центром задньої бабки. Частота обертання шпинделя повинна складати 1200 об / хв. Точіння циліндричних заготовок. |
|
Мал. 4. Прийоми обробки циліндричних заготовок Різець поступово подають вперед до торкання з обертової заготівлею, і в цьому положенні відводять його направо. За лімбу подають різець вперед на 2-3 ММІ роблять перший робочий прохід вздовж заготовки. Проходи здійснюють до отримання гладкої циліндричної форми (рис.4 а). Змістивши різець за показаннями лімба поперечної подачі до потрібного розміру, обточують невеликий пробний ділянку. Якщо завмер показав, що різець встановлений на потрібний розмір, то поверхню обробляють по всі довжині справа наліво (рис. 4 б). Після обточування різець відводять назад. І повертають у вихідне положення. Цим же різцем підрізають торець і уступи. Торець підрізають до зближення різця з центром деталі (рис. 4 в). Для протачіванія прямокутних канавок і уступів застосовують чистової (лопатковий) різець (рис.4 г). Переміщаючи його в поперечному напрямку і поздовжньо пересуваючи супорт, можна виточити циліндричну поверхню з різними діаметрами. Для вибірки отворів і внутрішніх порожнин деталей застосовують растачивание. Розточування виконують розточувальним наполегливою різцем (рис 4 д). Ріжучі кромки різця встановлюють на рівні осі шпинделя. При розточуванні подовжню подачу різця чергують з його поперечними зміщеннями від краю деталі до її центру, шар за шаром знімаючи матеріал зі стінки вирізується порожнини і вирівнюючи її дно. Точіння деталей складної форми виконують фасонними різцями |
|
Мал. 5. Варіанти заточування і установки фасонних різців Фасонні різці виготовляються самостійно з смуг вуглецевої або швидкорізальної сталі товщиною 3-5 мм, шириною 10-20 ММІ довжиною 100-120 мм. Різець обточують по нанесеному контуру, гартують і заточують (рис. 5 а). Різці повинні обов'язково мати затиловку бічних граней, щоб вони не стикалися з деталлю в процесі обробки (рис. 5 б). Можливі два варіанти установки фасонного різця (рис. 5 в) для прямого і зворотного точіння, при зворотному точении різець перевертають і отримують деталь зі зворотним профілем. Фасонні різці можна подавати на деталь в поперечному, поздовжньому напрямку і під кутом до осі деталі (рис.5 г). Для отримання деталей різного складного профілю можна використовувати складовою різець зібраний з різців товщиною 4-8 мм, з різною заточуванням. Їх різна комбінація дозволяє отримувати різноманітні профілю (рис. 5 д). Для отримання плавних форм як з зовні, так і всередині деталі можна використовувати різець з ріжучим диском. Диск товщиною 4-8 мм, діаметром 12-20 мм, по краю диска проточується канавка радіусом 2-3 мм. Після гарту диск встановлюють за допомогою бола на оправці і заточують (рис. 5 е). Обробка деталі по копіру. Великий обсяг однакових деталей зручно виготовляти за допомогою копіра. Як ріжучий інструмент, в залежності від конструкції верстата, можна використовувати токарні різці, встановлені в супорті верстата, стамески з упором або дискові фрези. |
|
Мал. 6. Обробка по копіру різцем і стамескою |
![]() |
Мал. 7. Обробка дисковою фрезою по копіру.
Точіння по копіру на супортні верстаті
Мал. 8. Обробка деталі по копіру
Для виготовлення копіра виточують модель деталі і розпилюють її уздовж осі. Отриманий зріз профілю переводять на фанеру товщиною 4-5 ММІ випилюють (рис. 8 а). Копіри можна виготовляти з металу за допомогою лазерного різання.
Профіль майбутніх деталей закріплюють на станині верстата. До поперечних санчатах супорта кріплять металевий тримач зі щупом. Вершина щупа і різця повинні мати однаковий профіль (рис. 8 б).
Першою заготівлі попередньо надають форму циліндра діаметром рівним найбільшому діаметру заготівлі, наступні заготовки можна робити з невеликим припуском. Спочатку налагоджують взаємне положення заготовки і копіра (рис. 8 в), потім супорт верстата зрушують вліво до суміщення вершини щупа з лінією найбільшого діаметра деталі (рис.8 г). Різець подають вперед до упору в поверхню заготовки, а щуп наголошують в копір в точці найбільшого діаметра і фіксують в цьому положенні. Обробку ведуть справа наліво. Різець подають на деталь в поперечному напрямку до упору щупа в контур копіра (рис. 8. д). Величина поздовжнього зсуву різця на один поперечний хід становить 1-2 мм. Сліди різання видаляють шліфувальною шкуркою. Один і той же копір можна використовувати для точіння деталей однакового профілю, але різного діаметру (рис. 8 е). Невелика зміна кута установки копіра дає звуження силуету деталі. Довгі деталі точать по копіру частинами. Симетричні фігури обробляють з краю до середини, потім заготовку перевертають і обробляють другу частину (рис. 8 ж).
Вибір режиму різання
Швидкість головного руху різання на токарних верстатах для різних точок ріжучої кромки різна і залежить від відстані до осі обертання заготовки. Середня швидкість для середньої точки визначається за формулою:
V ср \u003d πD cp n / (60 · 1000)
де D cp - середній діаметр заготовки, мм;
N- частота обертання шпинделя, об / хв;
Частоту обертання шпинделя вибирають в залежності від діаметра заготовки, при установці планшайби діаметром более400 ммчастота обертання шпинделя не повинна перевищувати 800 об / хв.
Швидкість головного руху різання для деревини м'яких порід 10-12 м / с, для деревини твердих порід 0,5-3 м / с.
Поздовжня подача на один оборот шпинделя для чорнової обробки 1,6-2 мм, для чистової НЕ более0,8 мм. Поперечна подача на один оборот шпинделя не повинна превишать1,2 мм.
Обробка деталей на токарних верстата з ЧПУ
Токарні верстати з ЧПУ, в якості ріжучого і інструменту мають кінцеві фрези або комбінуються кінцевий і дискової фрезами.
При обробці деталі кінцевий фрезою можна отримати різний фігурний профіль на заготівлі. Переміщення фрези і швидкість обертання заготовки задається за допомогою програмного забезпечення в залежності від форми майбутньої деталі.
Мал. 9. Створення скульптури на токарному верстаті з ЧПУ
Верстати з кінцевими і дискової фрезами, дозволяють прискорити процес точіння заготовок. Дискова фреза робить попередню чорнову обробку, кінцева фреза чистову.
Мал. 10. Обробка заготовки дисковою фрезою
Мал. 11. Обробка заготовки кінцевий фрезою
Після виточування заготовки, для остаточного доведення і видалення слідів різання, її обробляють шліфувальною шкуркою, зазвичай використовують шматок невеликої ширини, який переміщують в натягнутому стані по всій заготівлі.
Мал. 12. Обробка заготовки шліфувальною шкуркою
література:
1. Бурик В.Г., Власов В.Н. Домова резьба- М .: Нива Росії спільно з Компанією «Євразійський регіон», 1993-352 с.
2. Ветошкин Ю.І., Старцев В.М., Задімідько В.Т.
Дерев'яні мистецтва: навч. посібник. Єкатеринбург: Урал. держ. лесотехн. ун-т. 2012.
3. Глікін М.С. декоративні роботи по дереву на верстаті «Універсал» .- М .: Лесн. пром-сть, 1987.-208 с.
4. Коротков В.І. деревообробні верстати: Підручник для поч. проф. Освіти. - М.6 Видавничий центр «Академія», 203.-304 с.
5. Лернер П.С., Лук'янов П.М. Токарне і фрезерні справа: Учеб. Посібник для учнів 8-11 кл. середовищ. шк.-2-е изд., дораб.-М .: Просвещение, 1990.-208 с.
Точіння деталей циліндричної форми
На токарному верстаті виточують вироби, контур яких може складатися з декількох об'ємних геометричних фігур, Які називаються тілами обертання . Це фігури - куля, конус, циліндр і тор(Див. Рис. Зліва).
Точіння деталей на верстаті виробляють спеціальними різцями - токарськими стамесками
. На відміну від звичайних столярних стамесок, вони мають подовжені рукоятки, які дозволяють надійно утримувати інструмент і легше керувати ним.
За якістю обробки розрізняють чорнове і чистове точіння, від цього залежить і вибір інструменту.
для чорновий обробки застосовують напівкруглу стамеску (Див. Рис. а), Для чистового точіння, підрізання торців і відрізування деталі - косу стамеску (Див. Рис. 6 ).
при чорновому обточуванні заготовки (див. рис. а) Напівкруглу стамеску пересувають по подручніку. За перший прохід знімають стружку товщиною 1 ... 2 мм серединою леза стамески (див. Рис. 6 , зліва). Подальше точіння виконують бічними частинами леза при русі різця як вліво, так і вправо (див. Рис. 6 , Праворуч). В результаті роботи різними ділянками леза стамески поверхню деталі виходить менш хвилястою. Після 2 ... 3 хвилин роботи перевіряють надійність закріплення заготовки - підтискають її центром задньої бабки. На чистову обробку слід залишати припуск 3 ... 4 мм (по діаметру).
при чистовом обтачивании (Див. Рис.) Косу стамеску встановлюють на ребро тупим кутом вниз. Стружку зрізають середньої та нижньої частиною леза.
Токарну стамеску тримають при точінні двома руками: однією за рукоятку, інший за стрижень. За стрижень стамеску охоплюють зверху чи знизу. Для чорнового обточування частіше застосовується перший спосіб, як найбільш надійний. Натиск на стамеску повинен бути рівномірним і плавним.
Для виточування внутрішніх виїмок виробів з використанням патрона або планшайби(Різні ємності, шкатулки, сільнички і т.д.) - спочатку висвердлюють свердлом отвір по центру заготовки. Потім стамескою з напівкруглим кінцем вибирають зайву деревину. Наостанок, для вирівнювання стін, використовують стамеску з вигнутим кінцем (див. Рис. Зліва).
Для точіння виробів за допомогою планшайби спочатку роблять заготовку у вигляді квадрата. На цій заготівлі проводять діагоналі і креслять коло трохи більше, ніж діаметр передбачуваного вироби. Пилкою обрізають зайві кути до отримання восьмигранника, який прикручують до планшайбе шурупами. Планшайбу накручують на шпиндель і перевіряють - не чіпляє чи заготовка за підручник. Після цього верстат включають і восьмигранник обточують до потрібного діаметру. Потім підручник встановлюють паралельно площині заготовки і виточують її внутрішню частину. Пересунувши підручник, виточують зовнішню сторону вироби.
Діаметр вироби перевіряють кронциркулем
або штангенциркулем
. Заміри слід зробити в декількох місцях по довжині заготовки. Прямолінійність можна перевірити лінійкою або кутником на просвіт.
Відразу після обточування поверхню деталі зачищають шліфувальною шкуркою, прикріпленою до дерев'яного бруска (див. Рис.). Щоб яскравіше виділити текстуру деревини, поверхню виробу можна відполірувати бруском більш твердої деревини. Цю операцію виконують при обертанні деталі, так само як і шліфування.
При підрізання торців деталі косу стамеску встановлюють на ребро гострим кутом вниз і роблять неглибокий надріз (див. Рис. Зліва).
Потім, відступивши трохи вправо або вліво (в залежності від того, який торець підрізають), нахиляють стамеску і зрізають на конус частина заготовки (див. Рис. Справа). Цю операцію повторюють кілька разів, поки не залишиться шийка діаметром 8 ... 10 мм. Потім деталь знімають з верстата, відрізають її кінці ножівкою. Торці зачищають.
Для виготовлення великої кількості однакових деталей на токарному верстаті застосовують кондуктори(обмежувачі) Для стамесок або верстати з копіювальним пристроєм . Кондуктори нескладно виготовити самому і легко встановити як на токарної стамесці, так і на подручніке (див. Рис. Зліва).
Цифрами позначені:
1. - упор;
2. - обмежувач поздовжнього переміщення;
3. - обмежувач поперечного переміщення;
4. - токарна стамеска.
Для отримання потрібних контурів на що виготовляються деталях іноді застосовують і специфічні стамески (див.рис. Праворуч).
Їх іноді роблять спеціально для конкретного виробу або потрібного контуру.
Нижче наведено приклад вироби і стамесок, які використовуються для його виготовлення.
Наприклад, для виготовлення дерев'яного кульки використовують стамески, які виготовляють під конкретний діаметр (см. Рис. Зліва).
Без спеціальних стамесок цей же куля можна виточити і простими стамесками, але для точного виготовлення необхідно зробити трафарет (шаблон), за допомогою якого можна виміряти правильність сферичної поверхні.
Етапи виготовлення трафарету і точіння показані на малюнку справа.
Деревину для точіння готують, не тільки вирізаючи бруски або шматки дощок, а й використовують висушені гілки дерев, а також склеюючи шматки брусків або дощок (тобто. - із сегментів) (див. Рис. Нижче) .Нередко для точіння таких "блокових "виробів застосовують деревину різних порід.
Завдяки цьому, домагаються дуже незвичайних по фарбуванню і текстурі виробів.
При роботі дотримуйтеся таких правил:
Опустіть захисний екран (надіньте окуляри);
Перевірте роботу верстата на холостому ходу;
Обробляючи заготовку, плавно підводите різець;
Слідкуйте, щоб зазор між заготівлею та подручником не перевищував 5 мм;
Виконуючи осьовий свердління, ретельно закріпіть задню бабку;
Під час розточування внутрішнього отвору надійно утримуйте різець в горизонтальній площині;
Контроль розмірів і якості обробки робите при повністю зупиненій заготівлі;
При остаточній обробці деталі наждачним папером закріплюйте її на спеціальній державке.
Про всі несправності негайно повідомляти вчителя, попередньо вимкнувши верстат!
Після закінчення роботи:
Зніміть готову деталь з верстата;
Розкладіть інструменти і пристосування в спеціально відведені місця;
Проведіть прибирання робочого місця;
Повідомте черговому про закінчення роботи.
При роботі оглядового екран на верстаті повинен бути опущений.
Якщо на верстаті немає такого екрану, працювати треба в захисних окулярах.
Ріжучий інструмент підводять до заготівлі тільки після того, як шпиндель набере повне число обертів.
При включеному верстаті забороняється підправляти заготовку і вимірювати її розміри, переміщати вузли верстата.
Після виключення верстата не можна гальмувати руками заготовку, патрон або планшайбу.
Не можна залишати працюючий верстат без нагляду.
Після закінчення роботи слід покласти інструменти на встановлені місця, змести стружку щіткою.
забороняється:
Включати верстат без дозволу вчителя;
Працювати при відсутності огородження пасової передачі;
Використовувати непідготовлену заготовку;
Використовувати заготовку зі сколами, тріщинами, вологу або гнилу;
Спиратися на частини токарного верстата;
Класти інструменти та інші предмети на верстат;
Зупиняти заготовку руками;
Відходити від верстата, не виключивши його.
Навіть якщо ви нечасто працюєте на токарному верстаті, ці поради допоможуть навчитися швидко і просто виточувати будь довгасті деталі, затиснуті в центрах.
Перш ніж включити токарний верстат
- Якою б складною не здавалася виточена в центрах деталь, будь-яка з них складається з чотирьох базових форм, показаних на малюнку:валиків, прямих ділянок, напівкруглих і трикутних канавок, які можуть чергуватися в різних поєднаннях. Спочатку слід освоїти точіння кожної форми окремо, а потім можна почати змішувати їх, щоб отримати більш складний профіль.
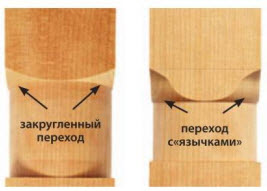
- Незалежно від застосовуваної різновиди різця використовуйте для формування базових форм одне або кілька головних рухів. Піднімайте ручку різця, щоб зробити проточку глибше або зменшити діаметр заготовки. Покачивайте інструмент з боку в бік при точінні напівкруглих канавок. Повертайте ручку різця, щоб знайти оптимальний кут різання при точінні невеликих форм. І наведіть різець вздовж підручника, обробляючи деталі по довжині.
Регулярно практикуючи на обрізаннях, ви зможете відточити майстерність володіння різцем, що допоможе зберегти цінні заготовки, і це не менш захоплююче, ніж точіння остаточної версії проекту.
Починаємо з квадратного перетину. точіння переходів
У більшості випадків заготовки для точіння в центрах мають квадратний перетин. Щоб надати їм циліндричну форму, встановіть їх в передній і задній центри токарного верстата і обробіть жолобчастим різцем-Рейєр.
Якщо на готової деталі повинен залишитися ділянку квадратного перетину, спочатку потрібно виточити перехід від квадратного до круглого перетину. Зазвичай переходи робляться закругленими або комбінованими (так званими «язичками»). Будь-який з них можна виточити Рейєр, але ми вважаємо за краще робити закруглені переходи косим різцем-Мейселем, так як при правильному використанні він дозволяє отримати більш чисту поверхню без сколів і виривів.
Якщо почати з виточування переходу, то в разі невдачі буде можливість повторити спробу, зупинити верстат і розгорнути заготовку кінцями на 180 °, щоб зробити перехід з іншого боку. А зіпсований ділянку потім буде Обточити до круглого перетину. Спочатку розмітьте верхню і нижню межі переходу на всіх чотирьох гранях заготовки. Якщо вона має товщину близько 75 мм, встановіть частоту обертання 1350 об / хв і сформуйте перехід, як показано на фото нижче. Закінчивши цей етап точіння, переходите до обточуванні решти заготовки, щоб надати їй циліндричну форму за допомогою РІЙЄРА.
Направте кінчик різця-Мейселя вниз і злегка торкніться ріжучої кромкою заготовки, відступивши близько 12 мм правіше нижньої мітки, і зробіть надріз глибиною 2 мм.
Зробіть кілька поглиблюються різів, з кожним разом пересуваючи різець ближче до нижньої межі переходу.
Дійшовши до нижньої позначки, починайте обертати різець за годинниковою стрілкою на 90 °.
Легкими рухами, зрізуючи матеріал потроху, сформуйте закруглення, що починається у верхній мітки і закінчується повною окружністю внизу.
Намітьте контрольні діаметри відрізним різцем
Зробіть розмічальні планку з упором-гачком на нижньому кінці і нанесіть мітки, що вказують положення всіх елементів профілю готової деталі. Перенесіть ці мітки на заготовку, як показано на нижньому фото.Потім за допомогою відрізного різця і штангенциркуля проточите контрольні діаметри.
Прикладіть до обертової заготівлі розмічальні планку, спершись її на підручник, притисніть упор-гачок до заднього торця і відзначте на заготівлі положення деталей рельєфу.
Налаштуйте штангенциркуль на необхідний діаметр, прикладіть в потрібному місці до гладкої частини обертається заготовки і починайте проточку контрольного діаметра. Коли губки штангенциркуля охоплять заготовку, відведіть різець.
Зробіть відрізним різцем контрольні проточки для всіх елементів, наприклад, для верхньої та нижньої частини несиметричною викружки, яка буде сформована в подальшому.
Формування трикутних канавок різцем-Мейселем
Вони робляться майже так само, як і закруглені переходи, але в цьому випадку різець не потрібно повертати. Так як обидві лінії профілю сходяться в одній точці, не потрібно використовувати відрізний різець для проточки контрольного діаметра. Замість цього по черзі подрезайте косим різцем-Мейселем обидві сторони трикутної канавки, як показано на фото.
Направивши кінчик різця вниз, відведіть ручку вліво, щоб фаска леза збіглася з кутом канавки. Торкніться різцем заготовки і підійміть ручку вгору.
Зробіть такий же легкий надріз з іншого боку канавки, відокремлюючи від дна вузьку трикутну стружку.
Роблячи рези поперемінно зліва і справа, поглибите і розширте канавку, щоб в її глибині вийшов необхідний діаметр.
Формування валиків жолобчастим різцем
Жолоби різці, що мають напівкруглий кінчик і неглибокий жолобок, відмінно підходять для точіння опуклих форм на зразок валиків. Почніть з розмітки центральної лінії валика (це можна зробити на попередньому етапі за допомогою розмічальної планки). Потім поступово скруглять черзі обидві сторони, роблячи рези від центральної лінії і починаючи їх все ближче до неї, як показано на фотоЗаокруглення з обох сторін не повинні торкнутися центральну лінію (олівцева розмітка видаляється на етапі остаточної шліфовки). Рухи різця зліва і справа повинні бути дзеркально симетричними.
Розмістіть різець желобком вгору, торкніться фаскою леза заготовки і зробіть легкий рух від себе і в бік від центру валика, одночасно повертаючи різець на чверть обороту.
Знімайте матеріал потроху, поки не сформуєте плавне закруглення від олівця лінії до нижнього діаметра або наступної форми.
Точіння напівкруглих канавок подібно формуванню валиків
Для точіння напівкруглих канавок-жолобків використовуйте таку ж техніку, як і при точінні валиків. Повертайте різець проти годинникової стрілки, формуючи ліву частину канавки, одночасно переміщаючи ручку інструменту вліво. Такі ж рухи, але в протилежному напрямку, робіть при точінні правій частині канавки.
Почніть роботу жолобчастим різцем, злегка повернувши його набік. Торкніться кінчиком різця заготовки і починайте піднімати ручку.
Робіть рези в напрямку дна канавки, одночасно обертаючи різець, відводячи і піднімаючи його ручку.
Продовжуйте роботу до формування середини канавки. Не захоплюйтеся, щоб не спотворити форму і не допустити появи відколів.
Залишилося тільки відшліфувати
Закінчивши формування деталей рельєфу за допомогою різців, видаліть їх сліди шліфуванням. Почніть з наждачного паперу № 120, а потім послідовно переходите до більш дрібнозернистої аж до № 220, якщо потрібно.
Шліфуйте інші круглі форми абразивами на тонкій паперовій основі. Вона дозволяє обробити поглиблення і легко рветься в разі зацепа, зберігаючи неушкодженими пальці.
Шліфувати круглі деталі на працюючому токарному верстаті набагато швидше, ніж вручну, але при цьому на поверхні залишаються поперечні ризики (фото 3). Щоб їх видалити, вимкніть верстат і додатково відшліфуйте деталь вручну, працюючи у напрямку волокон наждачним папером з поступовим зменшенням зернистості (фото 4).
Метод кріплення і установки заготовки у верстаті вибирають з урахуванням точності обробки, габаритів і жорсткості матеріалу. Обробка в центрах - це один із широко використовуваних методів точіння деталей на токарному обладнанні.
Коли застосовується кріплення до центрів
установка заготовки за допомогою оправлення: 1 - оправлення середня частина; 2 - лиска; 3 - центрові отвори; 4 - заготівля
- Так протачивают довгі деталі, у яких довжина п'ятикратно перевищує діаметр;
- якщо потрібно створити концентричність поверхонь під час фіксації;
- подальший етап точіння проходить на шліфувальному обладнанні;
- технологія не передбачає інші методи.
технологія кріплення
Заготівля фіксується в центрах з використанням спеціальних оправок. Для цього конус оправлення не повинен перевищувати 1: 2000. На підготовчому етапі в торцях деталі роблять центральні виїмки, в які будуть вставлені верхівки обох центрів. Оправлення обробляють мастилом і щільно натягують болванку. Для більшої щільності по кінця оправлення акуратно постукують дерев'яним чурбачков. Закріплення деталі в оправках такого типу може змінюватися в залежності від її діаметра.
Рух болванці передається за допомогою диску приводу, який надягає на різьблення шпинделя. Палець диску приводу примушує болванку до обертання. Цей метод більш небезпечний для оператора верстата, тому краще використовувати планшайбу повідкового типу з захисним кожухом. Болт закріплюють хомутиком, який спирається на лиску оправлення.
Установка заготовок з отворами (наприклад, зубчастих коліс або втулок) відбувається з використанням центрових оправок різноманітної форми. Один з типів оправок має шийку в формі циліндра, на неї надягають заготовку і закріплюють шайбою з гайкою. Гайка притискається до буртику і фіксує отриману конструкцію. Зліва за допомогою гвинта кріпиться хомутик. Деталь фіксується в верстаті для точіння виїмками на торцевих ділянках оправлення.
конструкції центрів
Центри для токарної обробки можуть мати різну конструкцію. Найпоширеніша є конус, на нього надівається заготовка, а також хвостовик конічної форми. Хвостовик повинен збігатися з отворами пиноли і шпинделя верстата.
Для закріплення заготовок із зовнішніми конусами використовуються зворотні центри. Конусоподібне закінчення має збігатися з серединою хвостовика. Щоб перевірити збіг в шпиндель вставляється центр і запускається на малих обертах. Про справність деталі говорить відсутність биття.
Задній центр найчастіше нерухомий, передній обертається з заготівлею і шпинделем. В результаті тертя виходять з ладу обидві поверхні, тому необхідно наносити мастило:
- крейди - 25%;
- тавоту - 65%;
- графіту - 5%;
- сірки - 5%.
Перед змішуванням необхідно розтерти в порошок без грудок сірку і крейда. Якщо не використовувати мастило, поверхні центрів зруйнуються, зміниться їх конфігурація.
Під час точіння заготовок на великих швидкостях центри швидше зношуються, збільшується отвір в торці самої деталі. Щоб зменшити руйнування заднього конуса на нього наплавляют зносостійкий шар.
Стандартний центр використовують при швидкостях до 120 оборотів в хвилину. Під час роботи з громіздкими і важкими заготовками на високих оборотах, при вибірці великої стружки жорсткості конструкції мало: деталь починає вібрувати і може віджатися.
обертається центр